When it comes to a workplace, you don’t need to work with combustible materials to face some serious risks. An explosion in a mine in West Virginia in the year 2010 killed 30 workers in the accident. It was an extreme incident of workplace hazard. From this, you must understand that every job comes with some potential hazards.
Some of the health and safety hazards commonly found at the workplace are workplace violence, chemical exposure, communicable disease, ergonomic injuries, transportation accidents, etc. While some of these can be prevented by powered air purifying respirator papr, others can’t. Also, it has to be noted that all these hazards are not likely to happen at every work space. When it comes to such hazards, some may turn out to be costly for the business, while some may affect the health of its employees. So the company needs to study which hazard can affect its employees and business in the long run. A proper planning and its execution can help to keep the business and employees safe from such health hazards.
OSHA – Occupational Safety and Health Administration, which is a part of the federal government to ensure health and safety laws, is responsible for taking the required legal actions, when it comes to an industry or state. It has become more vigorous and strong after the recent hazards at workplaces, including the one that took place in the mine of West Virginia. Many believe that it is good to be on the side of OSHA and do the needful to protect the employees from safety and health hazards. The steps may be costly at the initial level, but then the saying goes “prevention is better than cure”. You may sign up for osha 10 online classes and make sure you’re compliant at all times.
Continuity management
DRII executive director, Al Berman says that when it comes to small or medium sized businesses, something that affects the larger part of the workforce will eventually affect the business with more impact as compared to larger businesses.
One of the common hazard at a work place is communicable disease such as flu or cold. This may affect the larger portion of the crowd if not controlled. One of the main reason for its spread is the presence of infected employee at the work place. Berman says that no company discourages a sick employee from coming to office. Moreover, less number of sick leaves pushes the sick employee out of the bed.
Instead of increasing the number of sick leaves, the company can make an arrangement so that the employee can work remotely. For this employee needs to have access to company system and e-mail accounts. When it comes to field work, this kind of arrangement cannot work as employees are expected to be on the field to get the job done.
Something else that the employer can do is to train the employees with multiple tasks. This way absence of one employee will not affect the working of the department. This may cost the company time and money, but it can turn out to be a long term investment.
Get ready
Hazard analysis and risk mapping are the two general ways by which an employer can get ready to face any safety and health hazard at the workplace. This is process by which company needs to check the routine procedures and find out the underlying risks.
Look out for fatalities
When it comes to workplace hazards, many a times, employees don’t actually die at the workplace. Fatalities caused by driving is one of the biggest fatalities related to workplace. Many a times, it is caused by sleep deprivation, overwork and talking on a cellphone. Neille Brown, director of Workplace Health & Safety Programs at the School of Industrial Labor relations, Cornell University states that employees need to have regular working hours. Another important thing that an employer must look is to help the employees have proper work-family balance.
Less serious injuries
When it comes to less serious injuries at the workplace, they are often related to the ergonomic injuries. They may not prove fatal but may create chronic conditions. This can cause reduced productivity. Brown adds that ergonomic injuries can not only be caused by using older company equipment but also by sitting at a place for a long time.
One of the ergonomic injury that is quite more prevalent in the manufacturing industry is hearing loss. This can be prevented to an extend by providing earplugs or headphones to the employees. Simply providing the earplugs are not enough as company needs to ensure that the employees are using the protective gears for their safety.
The Human resource department of the company can reduce the workplace hazards to a large extent by educating the employees. For this, all they have to do is to send a monthly mail to the employees and let them know about the hazards that are related to the particular work environment. This takes very less time, but can prove very useful. Some of the preventive measures require training. So they should make sure that the employees are trained and sessions are documented regularly.
Berman adds that companies should consult the industry experts and discuss the type of hazards that are associated with the field. They must try to get an expert review on the precautions that can be taken at the workplace to avoid such accidents.
Freya Lowe is an expert blogger with a strong passion for writing. In her leisure time, she really likes to share her views and her trips to various places.
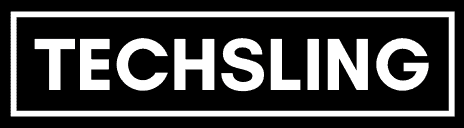